Inventory Management
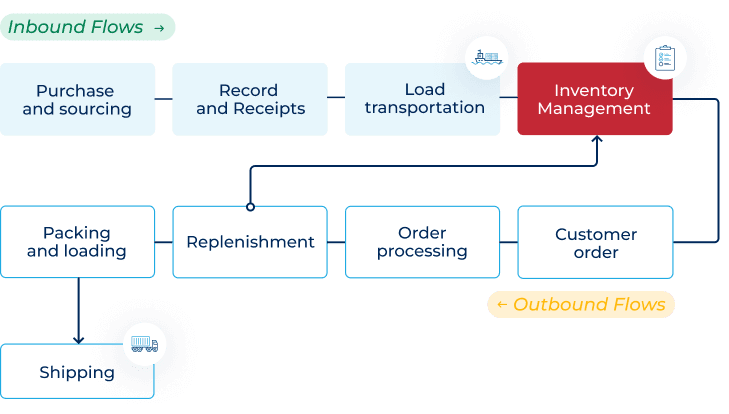
Efficient inventory management and a smooth supply chain are vital. Businesses must ensure that they have the right products, in the right amounts, at the right time.
Poor inventory management can result in a string of disasters, with customer orders going unfulfilled and delivery dates not being met.
Strong inventory management resides in the ability to monitor, predict and orchestrate inbound and outbound flows.
Ultimately, reducing CO₂ will help your organization positively impact the planet, make happier customers, and reduce costs. BuyCo is here to partner with you and give your organization the tools you need to not only measure but more importantly reduce your carbon container freight carbon footprint.
One way to mitigate the risk of inventory outages is to augment safety stocks, resulting in significant storage and working capital costs.
One key information to limit safety stocks is transportation lead time, which plays an important role in planning reorders and thus in inventory management as a whole. For businesses, safety stock requirements are defined by how close they control the lead time. The level of safety stock augments with the lead time but more significantly with the uncertainty on lead time.
Companies usually have a good level of control for what they manage internally, customer service, production, order processing and inventory lead time. But they usually have low control over the transportation lead time even for intra-company flows, specifically when they outsource the shipping process. They do not have a full control of the time it takes for goods to be shipped from the production site to wearhouse.
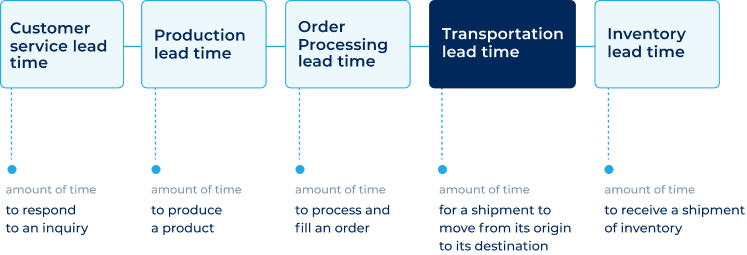
BuyCo container shipping platform enables businesses to control the lead time by selecting the vessel on which their products will be shipped, limiting the uncertainty on delivery date and augmenting the capability of stock planning. This ability can tremendously impact the safety stock requirements and costs, whether you operate your shipments, or their are operated by your 3PL or your supplier.
Why lead time is central to inventory management
Lead time in inventory management is the amount of time between when a purchase order is placed to replenish products and when the order is received in the warehouse.
Lead time is a central pillar of inventory management. Businesses must ensure that they have a solid understanding of lead time and that they can keep it under control. Otherwise, there could be serious knock-on effects, with ensuing delays for customers.
Indeed, if lead times start to get out of control, this can come to form a vicious circle, with lead times growing steadily worse as the supply chain seizes up thanks to the increased number of units required. This can then lead to longer delays for consumers, causing lead times to deteriorate further.
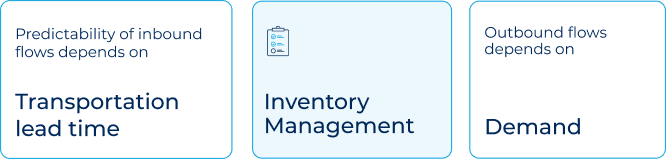
Poorly-managed lead time can mean that stocks run out and customers can’t get their orders fulfilled. Inadequate order management can do a great deal of damage to businesses’ reputations, causing them to lose custom to competitors. It is essential, therefore, that you do everything you can to control lead times as effectively as you can.
Impacts of lack of control on lead time transport element
When suppliers struggle to deliver a purchase order on schedule and in the right quantities, it can cause serious problems to a business’s workflow. It leaves businesses with only their existing, on-hand stock with which to fulfill orders; if this stock proves to be insufficient to meet customer demand until new stock arrives, customers will face delays or unfulfilled orders.
Lead time can have a significant impact on the customer experience. Consumers have a lot of choice at their disposal now, and it’s easy for them to take their custom somewhere else if they have a bad experience with a retailer. If their orders are delayed or they can’t find what they want, they’re likely to seek alternative outlets.
Furthermore, if lead times are persistently too long, storage costs will likely be higher as businesses will need to store higher levels of inventory so that they’re prepared for demand. This will increase product pricing and render businesses less responsive; introducing new products is made more difficult as existing stocks are harder to shift.
Why don’t most shippers control Transportation Lead Time?
Uncertainty in lead time causes requirements for higher safety stocks, and associated costs. But businesses do not control the transport element of the lead time because they outsource shipping to 3PLs or buy under CIF incoterms without selecting the vessel and the arrival date.
This is a real life example for a FMCG business.
Once the requirement for safety stock refill has been identified, the company send a transport requirements to a Freight Forwarder/3PL/supplier that will manage the shipment.
The Freight Forwarder has the instruction to book the shipment within a 2 weeks window. And the transit time for this trade can vary from 4 to 6 weeks. Between the earliest booking and the shortest transit time option, and the latest booking and the longest transit time option, there is an uncertainty on delivery of 4 weeks.
This delivery date uncertainty generates a safety stock requirement of 96 days.
What are the benefits of controlling the lead time and how can you achieve this?
With BuyCo a company can actively select the vessel schedule for their shipments, whether they book directly within shipping lines, or it is a Freight Forwarder/3PL who is doing the booking. Because they do so, they have full control on the date of departure, and more importantly on the date of arrival of the containers.
This enables businesses to limit dramatically the requirement for safety stock, because they can accurately forecast their inbound flows.
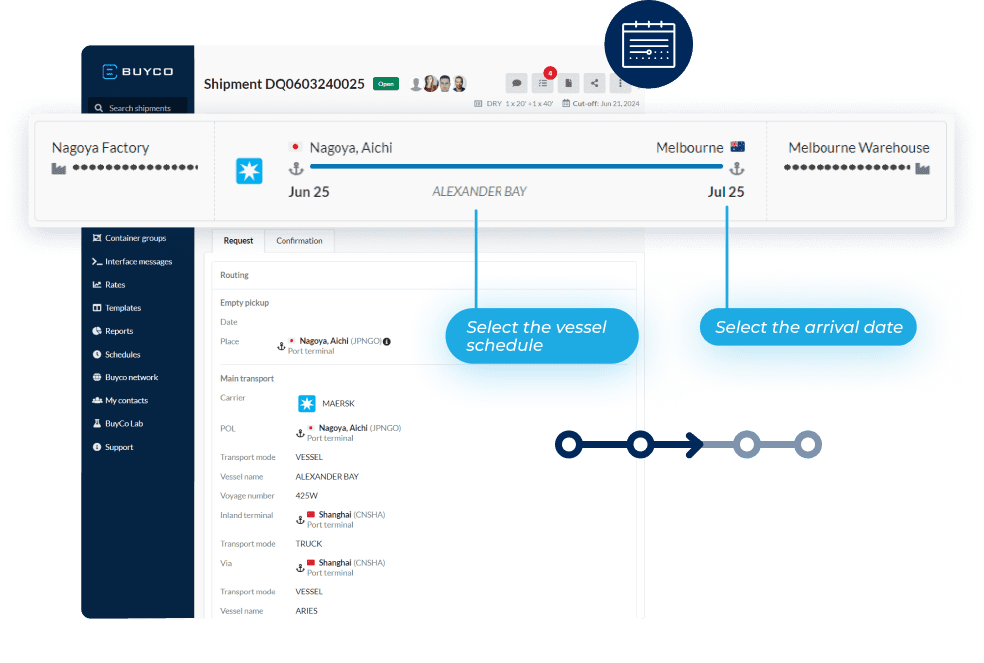
In our example a company with 4 weeks of delivery uncertainty would need 96 days of safety stock and with BuyCo schedule selection, they can reduce the delivery uncertainty to only 1 week. They can cut their safety stocks requirements by more than 2 weeks.
This results in large savings in terms of storage, inventory management complexity and working capital.
The same benefit applies in a world of supply disruptions such as the the Red Sea crisis. Some vessels will sail through the Red Sea with a shorter lead time but higher risk of delay, and some others through the Cape of Good Hope with a longer lead time but lower risk of delay. Inventory management is more efficient with longer transit time but more predictable flows.
Relying on your Freight Forwarder, 3PL or supplier to select the vessel and routing (Red Sea or Good Hope) increases your lead time uncertainty, and the requirement for safety stocks.
Using the BuyCo platform for container flow management allows companies to select optimal schedules and routes that align with their inbound flow cadence. They communicate their chosen option to transport partners for efficient booking and operation in line with the business requirements.
Quick and easy way to estimate potential savings
Getting control on vessel selection has a direct impact on lead time uncertainty reduction and by consequence a reduction in the safety stock requirement.
Let’s identify the ROI order of magnitude through an example.
With 100 M€ in sales and a COGS of 50%, equating to 50 M€ in annual purchases (100 M x 50%), the company currently spends 960k€ each week on buying.
A reduction in safety stock by one week can lead to substantial savings:
- Immediate savings of 961,538€ from reducing safety stock by one week
- With a cost of capital of 10%, the company stands to save 96k€ annually (961,538 x 10%) on working capital
- The potential savings from managing a smaller inventory cannot be accurately estimated as it varies based on the company’s specific operations.
By implementing these changes, the company can not only streamline its operations but also enhance its financial performance in the long run.
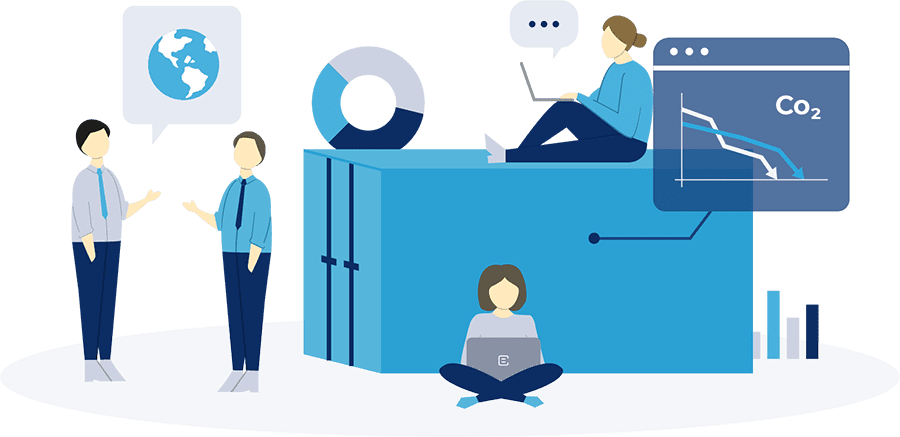
Ready to streamline your inventory management?
Discover how BuyCo can help you control inbound flows to cut safety stocks requirements and associated costs.